Lignor’s Products have a plethora of uses and a unique role to play as the world moves to a carbon constrained economy.
When Graeme Black first joined the Lignor Board, he was offered Lignor samples the size of phone directories or door stoppers. He thought conversely; Lignor samples had to be useful practical everyday items, which you could carry around in your pocket or hand-bag to show their versatility. So as a keen carpenter since he was 8, he was eager to illustrate how appealing, machinable and versatile Lignor is, using conventional wood working tools and techniques.
Lignor Eucalyptus products easily substitute hardwoods for many internal uses. Graeme was most concerned how so many hardwoods had became threatened around the world. He was part of the regenerative Craigpine Timber Board in NZ that voluntarily stopped cutting hardwood native forest in NZ in 1987. Craigpine then focused on Pinus radiata, eventually exported to 22 countries. Craigpine was the first entity in Australasia to get FCS accreditation in 1997, merely 4 years after FSC’s formation in 1993.

Graeme had witnessed the pitfalls of conventional paper- based accreditation audits in certain parts of the world. As an engineer, he was keen to have a more rigorous scientific, irrefutable proof of the timber’s legal provenance. Simmonds Lumber Pty Ltd, another Black Family owned company of which Graeme was a director, was seriously concerned that its main tropical hardwood must be independently audited to prove it came from a legal source.
Simmonds chose to raise the accreditation bar and fight against illegal logging. Hence in 2007 Simmonds became the first company in the world to prove its timber was legally sourced using independent DNA auditors (Certisource/Double Helix Pte Ltd). This pioneering technology made news from the BBC to The Economist, WWF and Greenpeace. Such articles illustrated such technology definitively helps fight illegal logging which Interpol believes accounts for some 30% of the world’s timber supply. What other industry would put up with such a high piracy rate?

Provenance of eucalyptus is not nearly such an issue being already widely certified and accredited. Eucalyptus has migrated across to the world being the most planted and fastest growing hardwood in the world covering some 20 M Ha in 86 countries.
Graeme’s vision was Lignor becoming the IP portal converting this abundant global resource into value-added engineered wood solutions and substituting for more precious and scarcer timber and higher embodied energy construction products. Much of this eucalyptus had been planted for pulp and paper but demand has reduced due to uptake of electronic communications & media.
So inspiration took hold and Graeme set out to hand make hundreds of Cross Laminated Strand Timber (CLST®) coasters, and pens. The 3 layer coasters have been frequently described as the best business card in the room. Made by cutting c 2.5mm thin wafers of Lignor Engineered Strand Lumber (ESL) across its longitudinal axis so that the strands resemble wood grain patterns. He then cross-laminates three wafers and bonds them with polyurethane glue bought from most DIY shops.
The 3 -layer CLST is trimmed sanded and varnished. The final touch is decoration with Lignor logo and product info.
These coasters and their former versions, made from Lignor container boards tested by Maersk, went to many people including Sir David Attenborough and Princess Laurentien of the Netherlands. Both these dignitaries are keen conservationists and patrons of Flora and Fauna International.
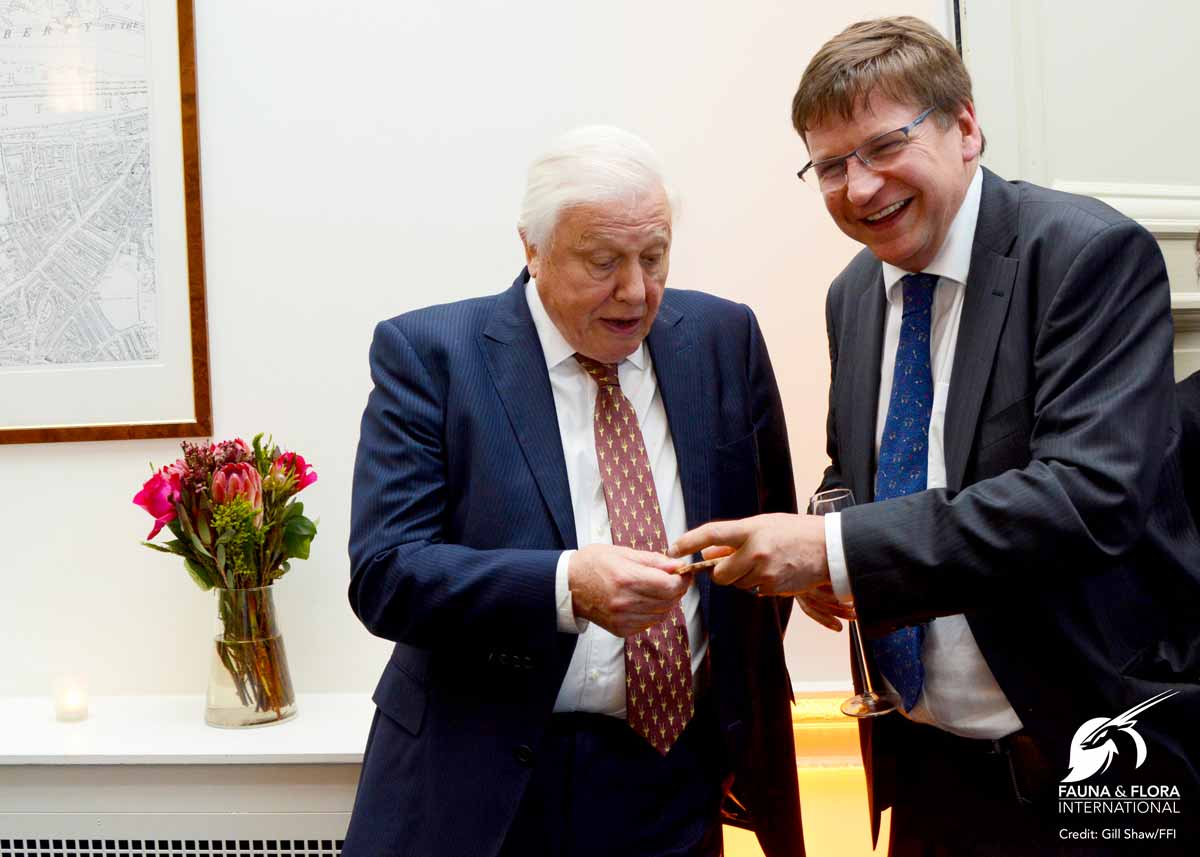
Pictured: Sir David with coaster made for former Lignor container floor tested at Maersk’s R&D centre at Tinglev, Denmark
Lignor worked with Maersk on this project as it was concerned that decades ago nearly all the container floors were made of tropical rainforest timber. Harvesting younger and younger timber was not only becoming environmentally unsustainable but yielded structurally weaker products. After a few years Lignor’s product passed the most rigorous ISO 7.26 tonne dynamic test at Maersk’s R&D test centre in Denmark.
Lignor has since made a container floor out of 7 year old Eucalyptus that is stronger than one made out of 70 year old tropical rainforest.
The Lignor pens and biros are made with the help of a kit pen which contains all the pen hardware parts. These kits include a brass barrel tube which is glued longitudinally into an appropriately sized block of ESL. When the glue is dry, the block is turned on a lathe until the outer Lignor layer is about 1 mm thick. The kit is then assembled around the Lignor encased brass tube.
Like many things in life, Graeme learnt from his failures when the Lignor separated from the brass tube in the turning process. Initially the failure rate was close to 40%, but after adopting 10 key steps he was able to reduce the failure rate down to less than a few %. Even then the failures were mostly retrievable. He has passed on these tips to his subcontractors.